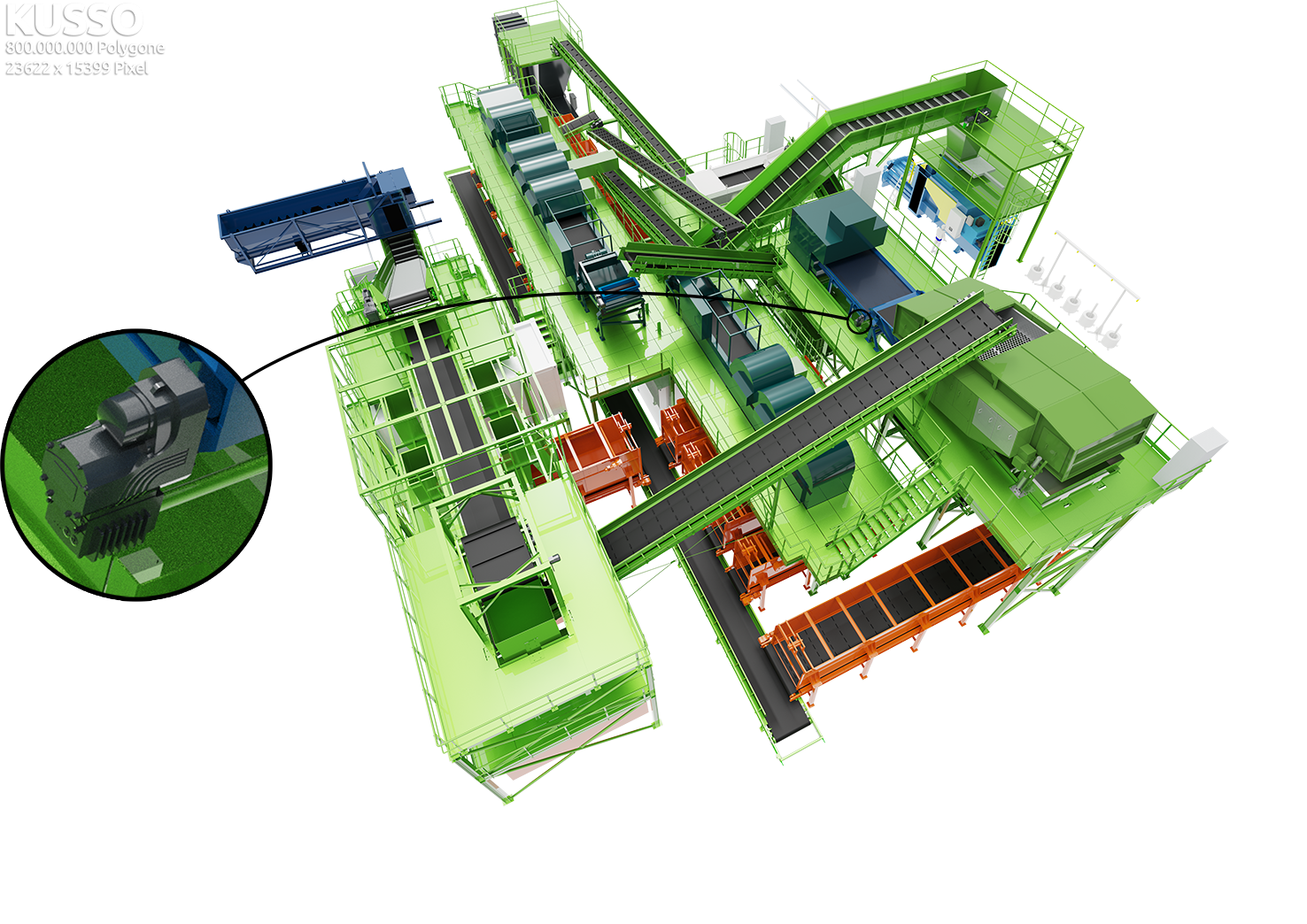
In 2022, I joined the rollout of KUSSO, a next-generation plastic sorting facility just outside Prague. This wasn't just another plant – it was the first installation of its kind and scale. Which, as you might guess, came with a few... surprises.
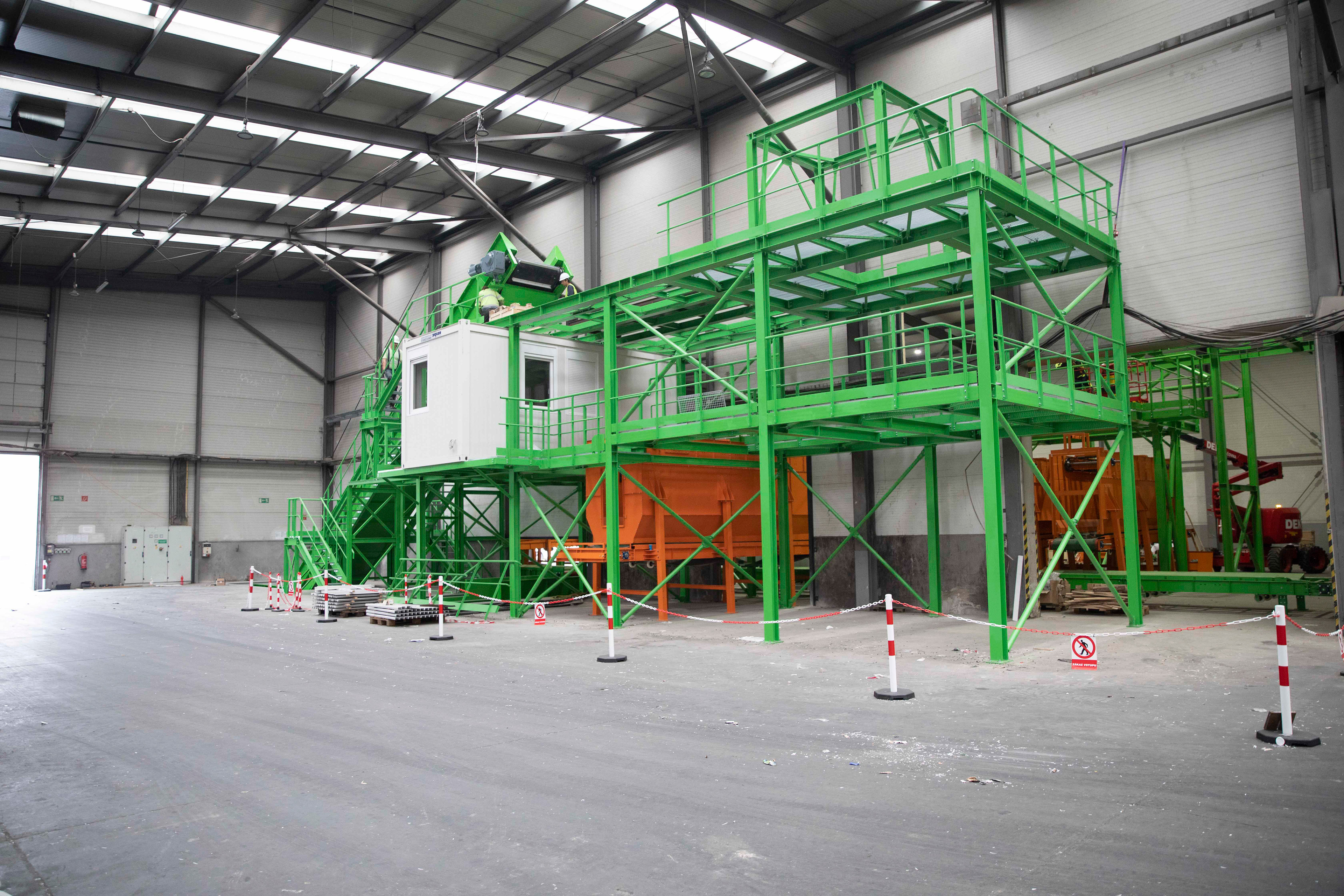
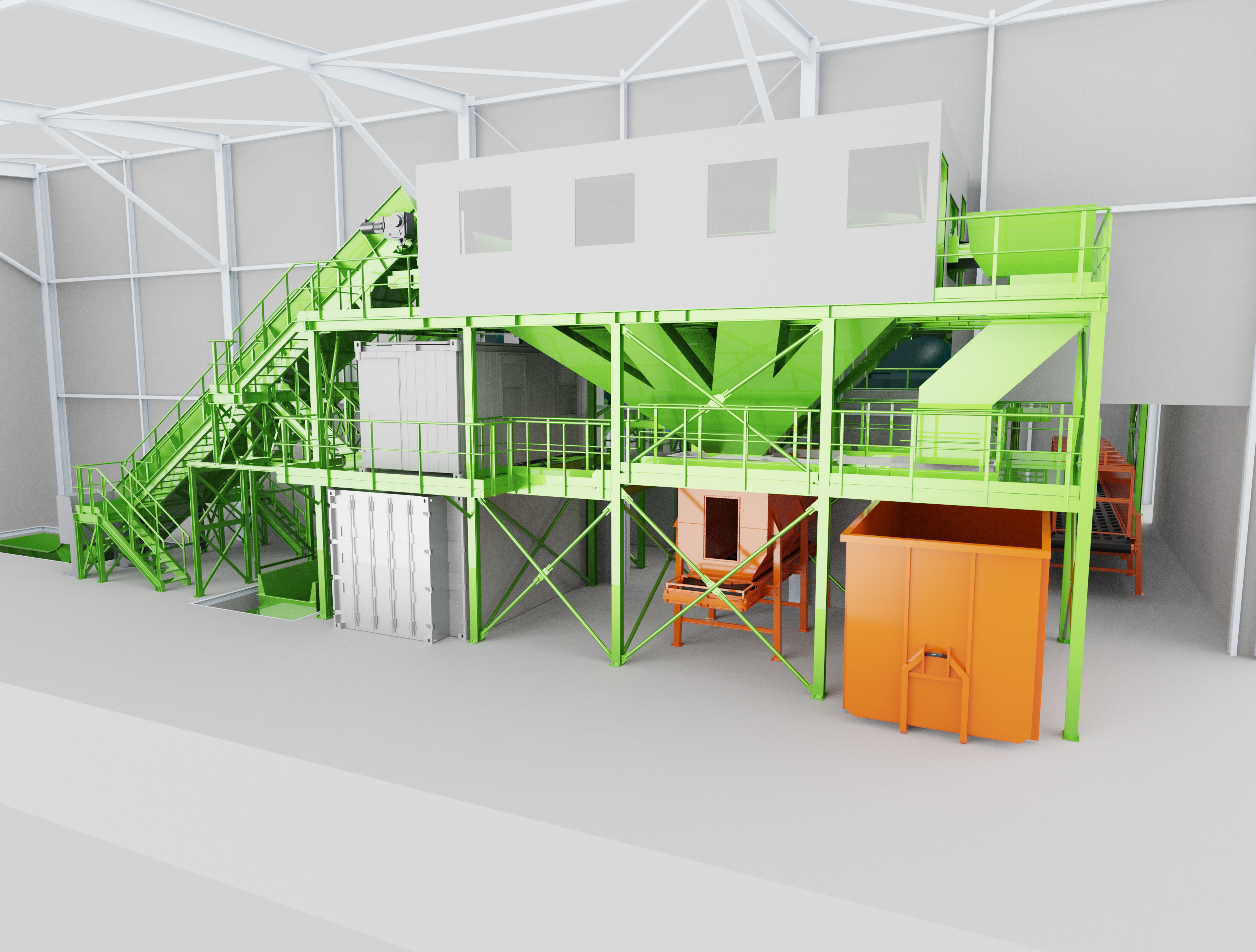
Originally brought in to observe and report, I quickly became a kind of on-site Swiss Army knife. From engineering diagnostics to pest control – we had it all.
A detailed animation visualizes the complete material flow: from the initial bag opener, across conveyors, through magnetic separation, and into the final sorting stages – step by step, just as it happens in the plant.
Operational Issues? No!
Early on, the system faced significant challenges: birds nesting in the ceiling and fouling up (literally) sensitive equipment, process engineering misalignments, and unexpected wear across several machines. I documented everything in detailed reports – not just for the sake of logging issues, but to help the team move forward with concrete, actionable solutions.
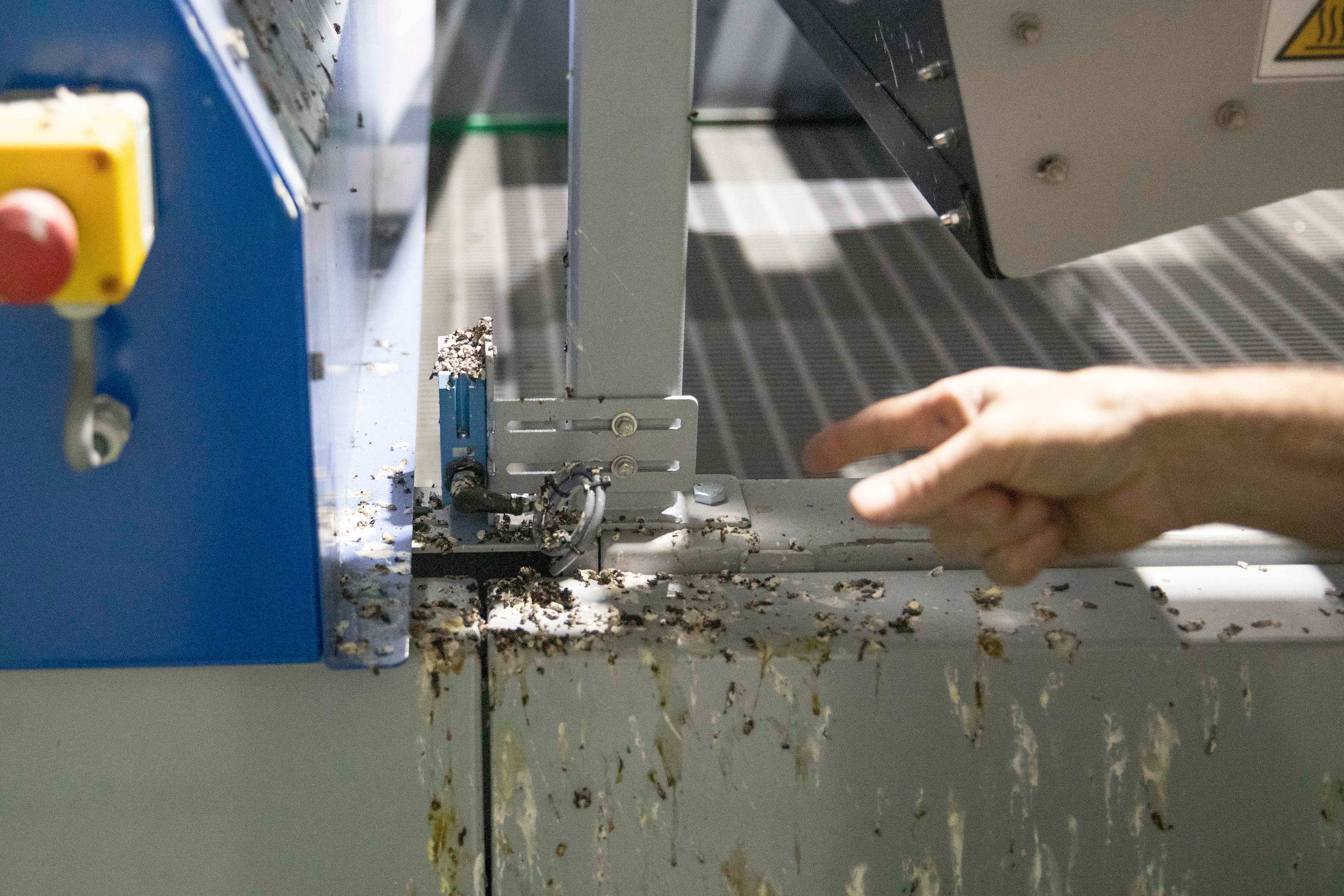
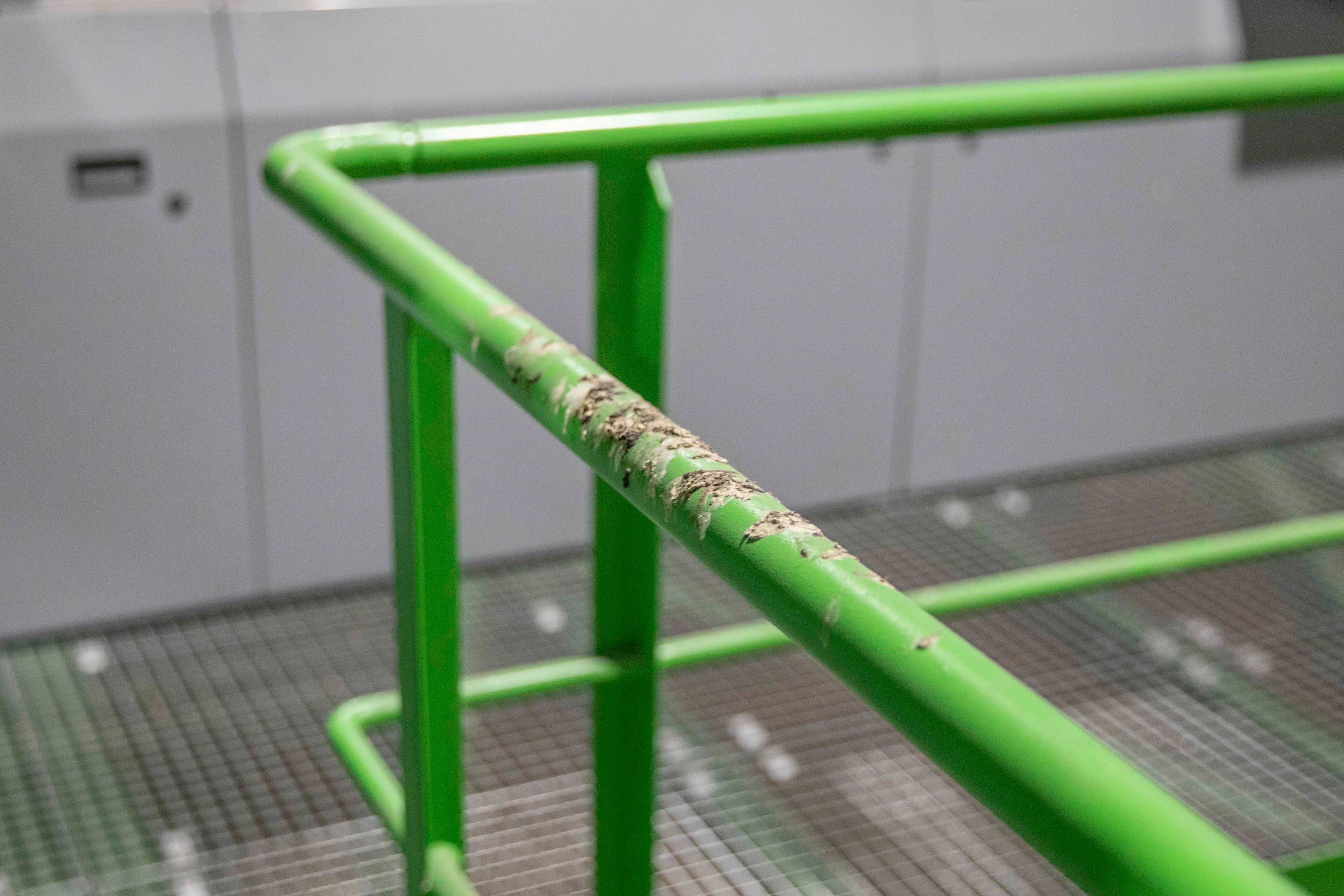
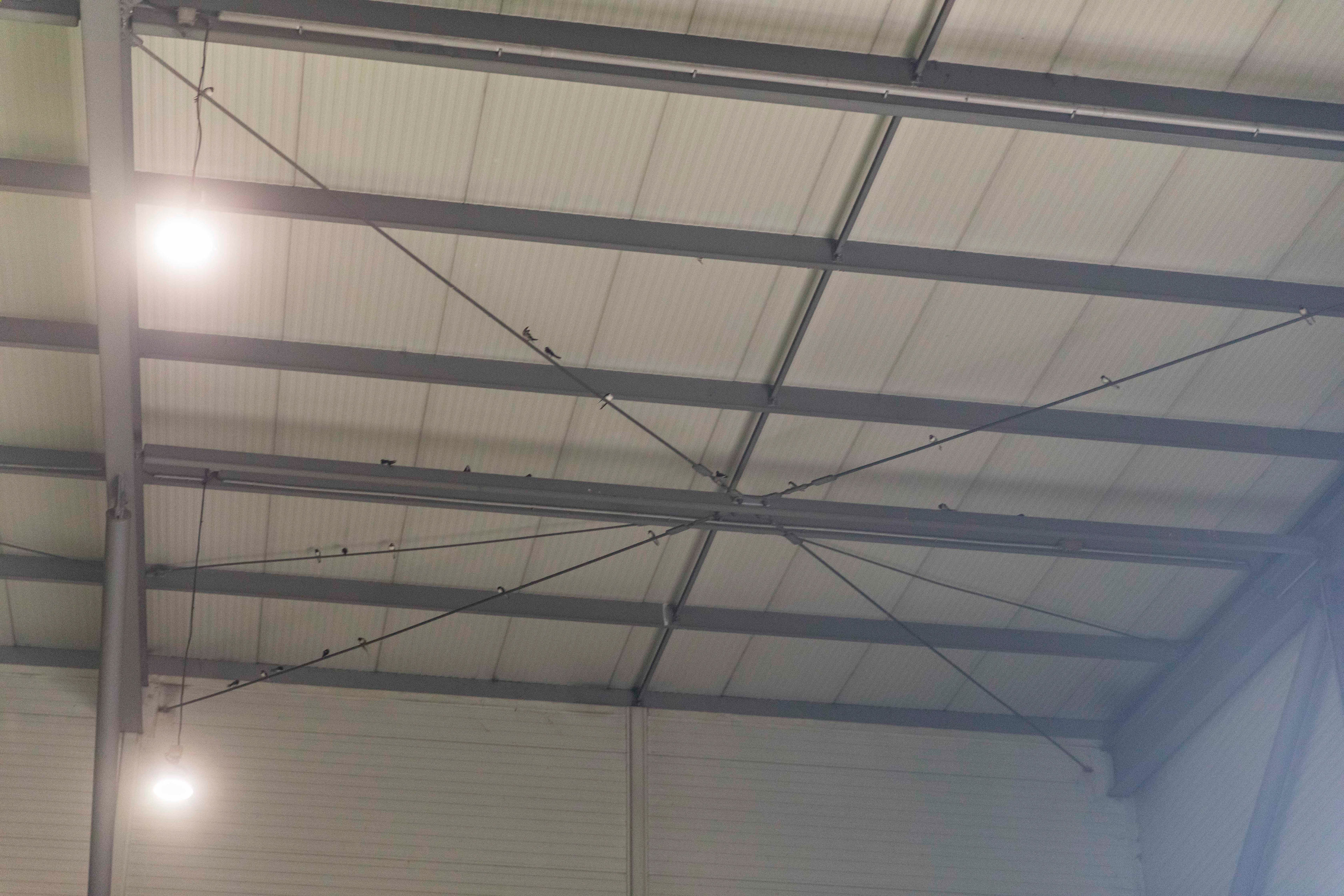
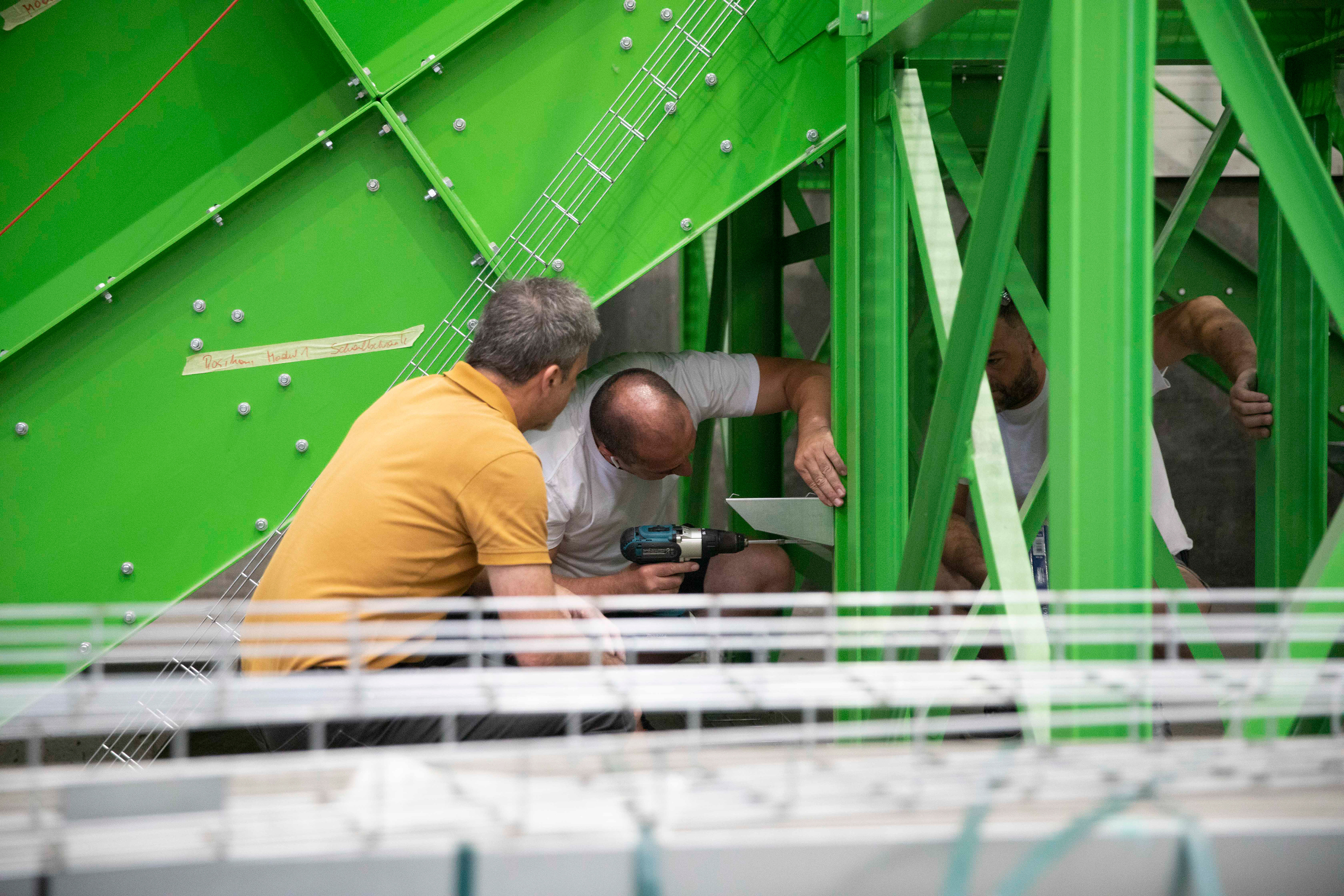
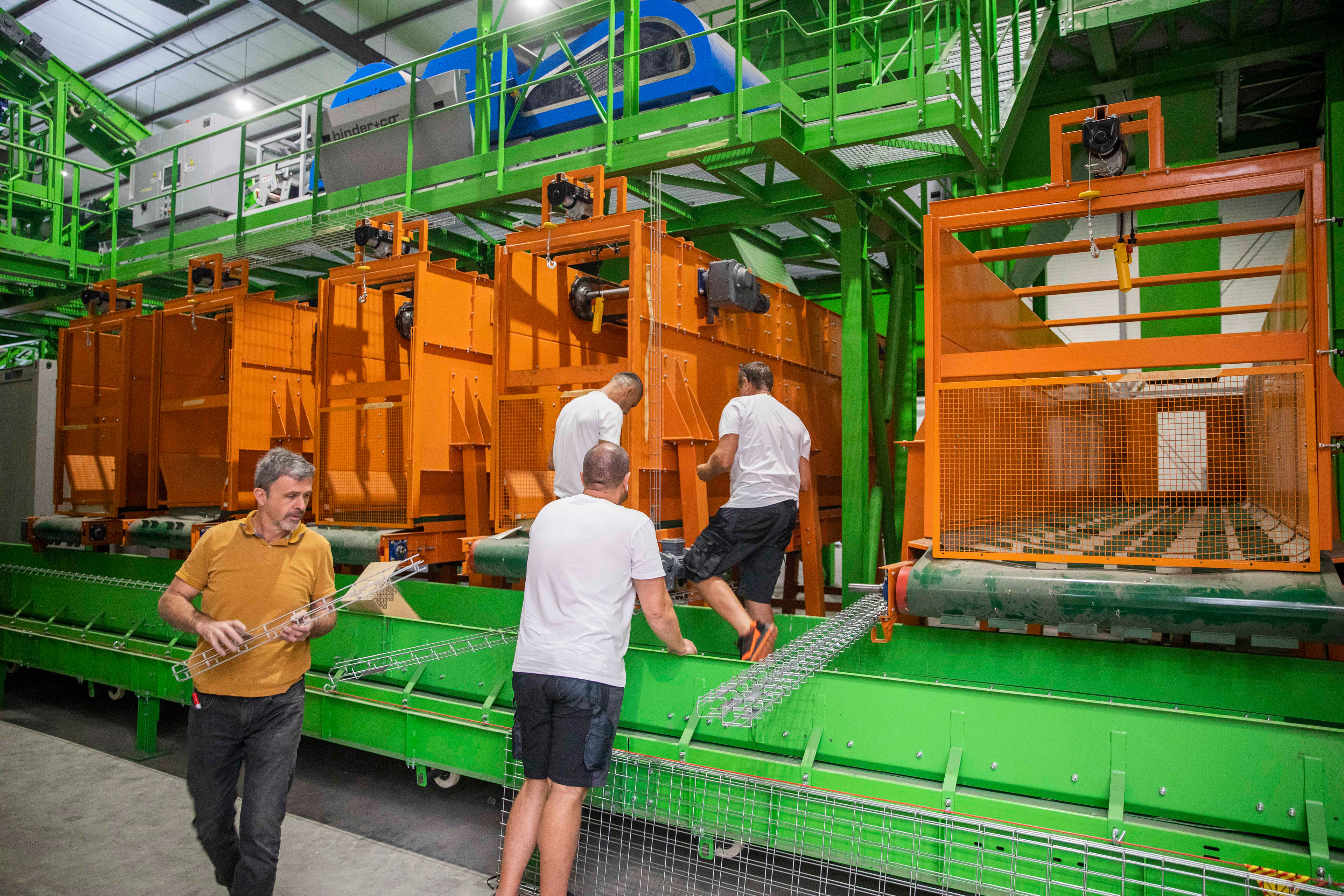
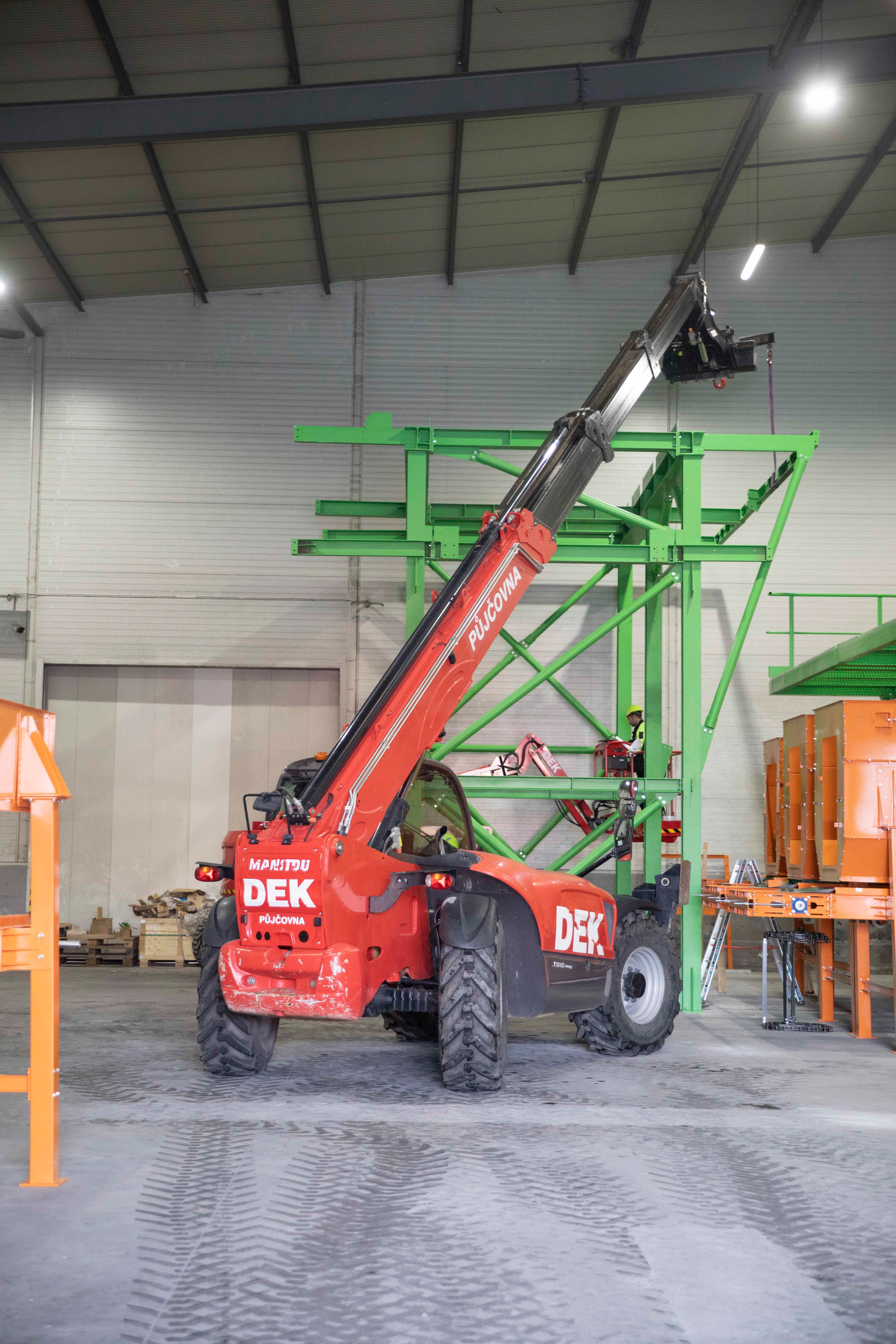
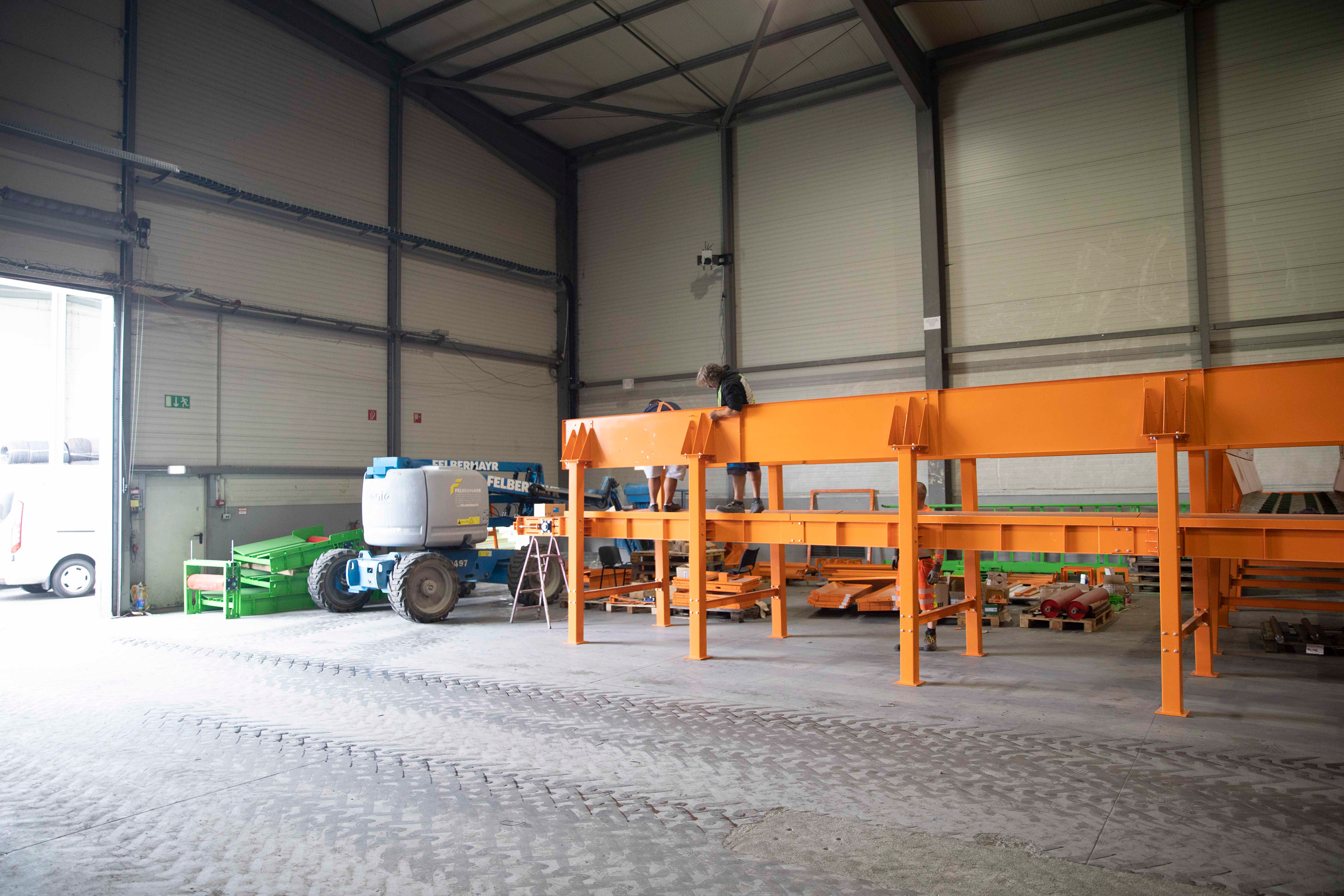
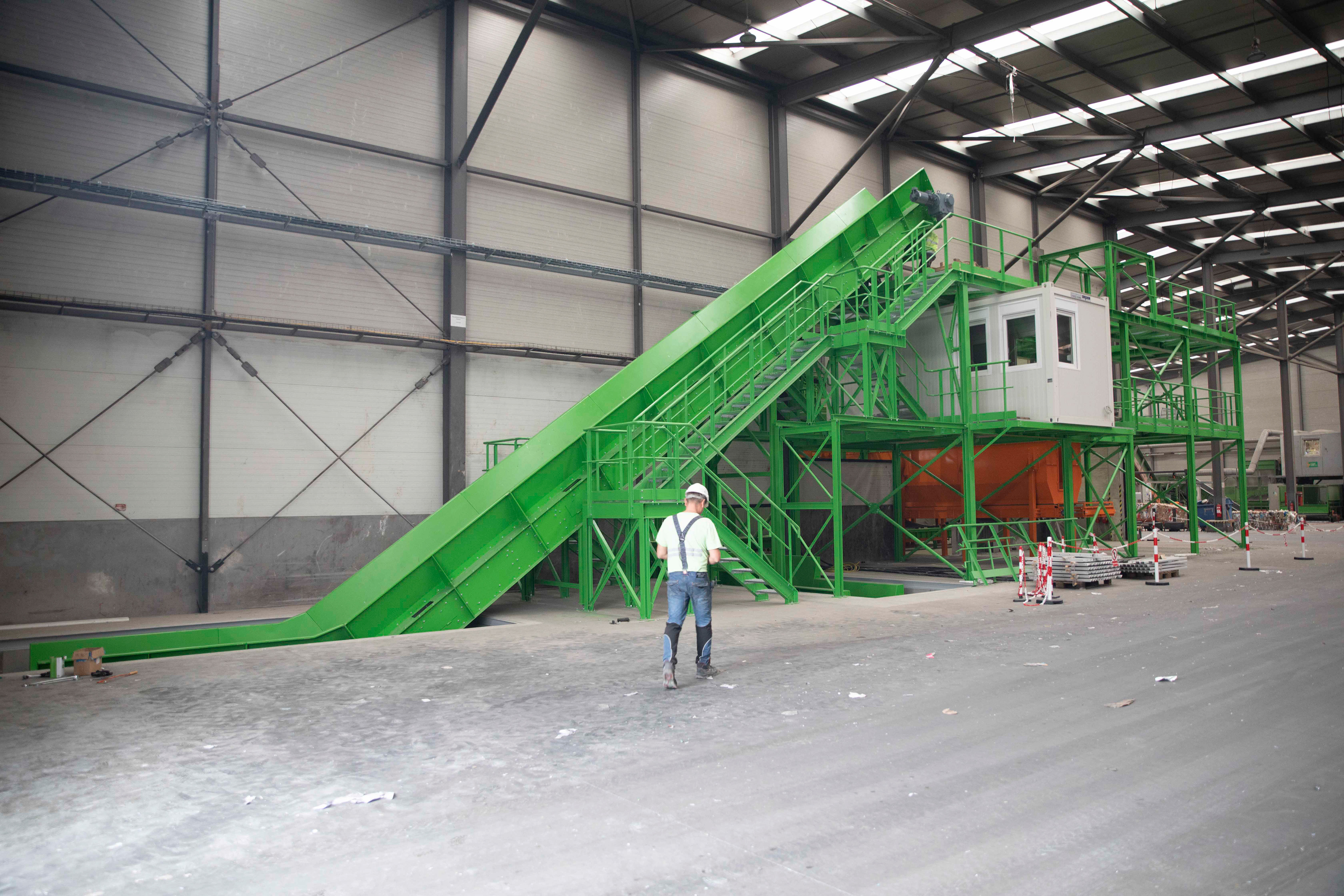
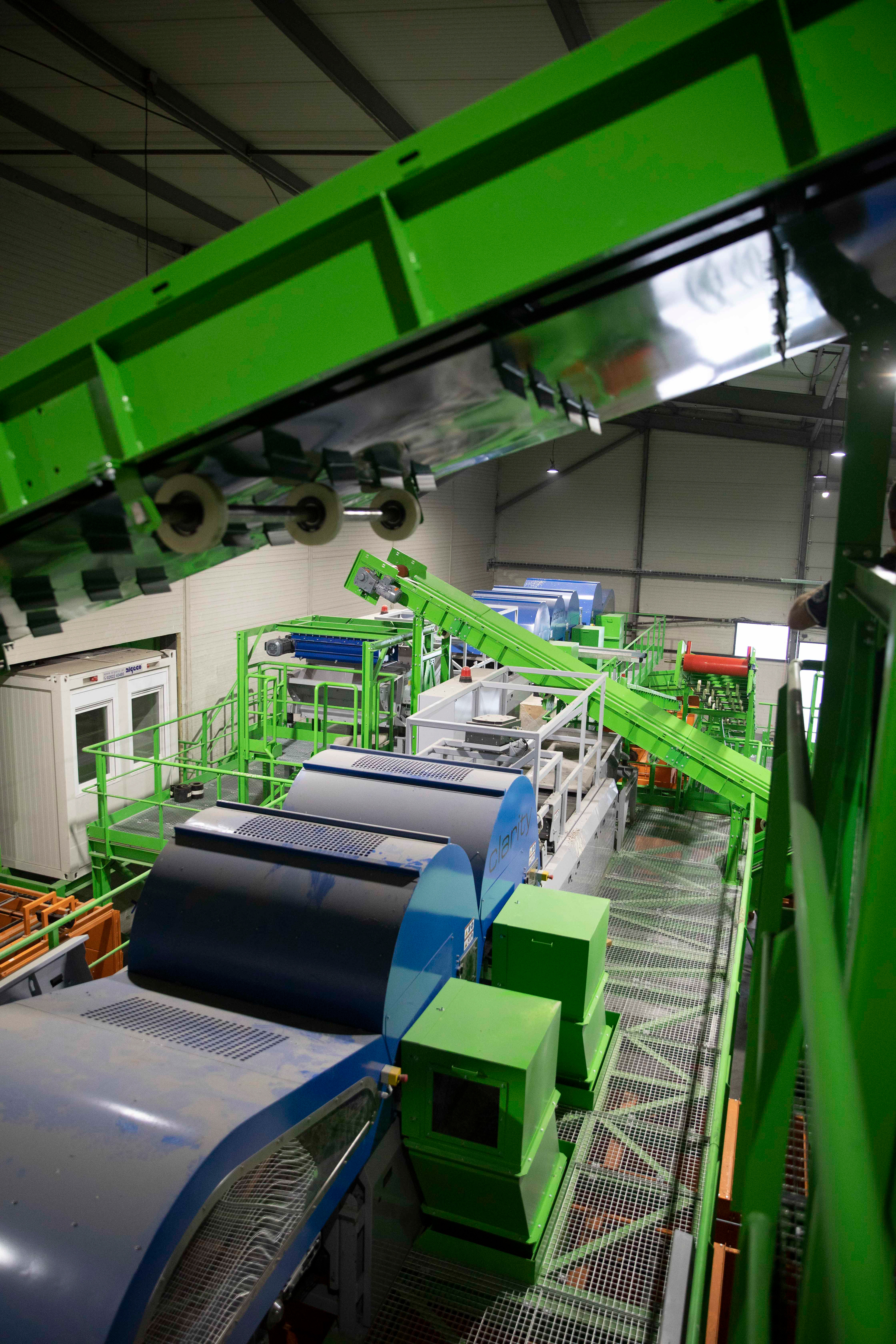
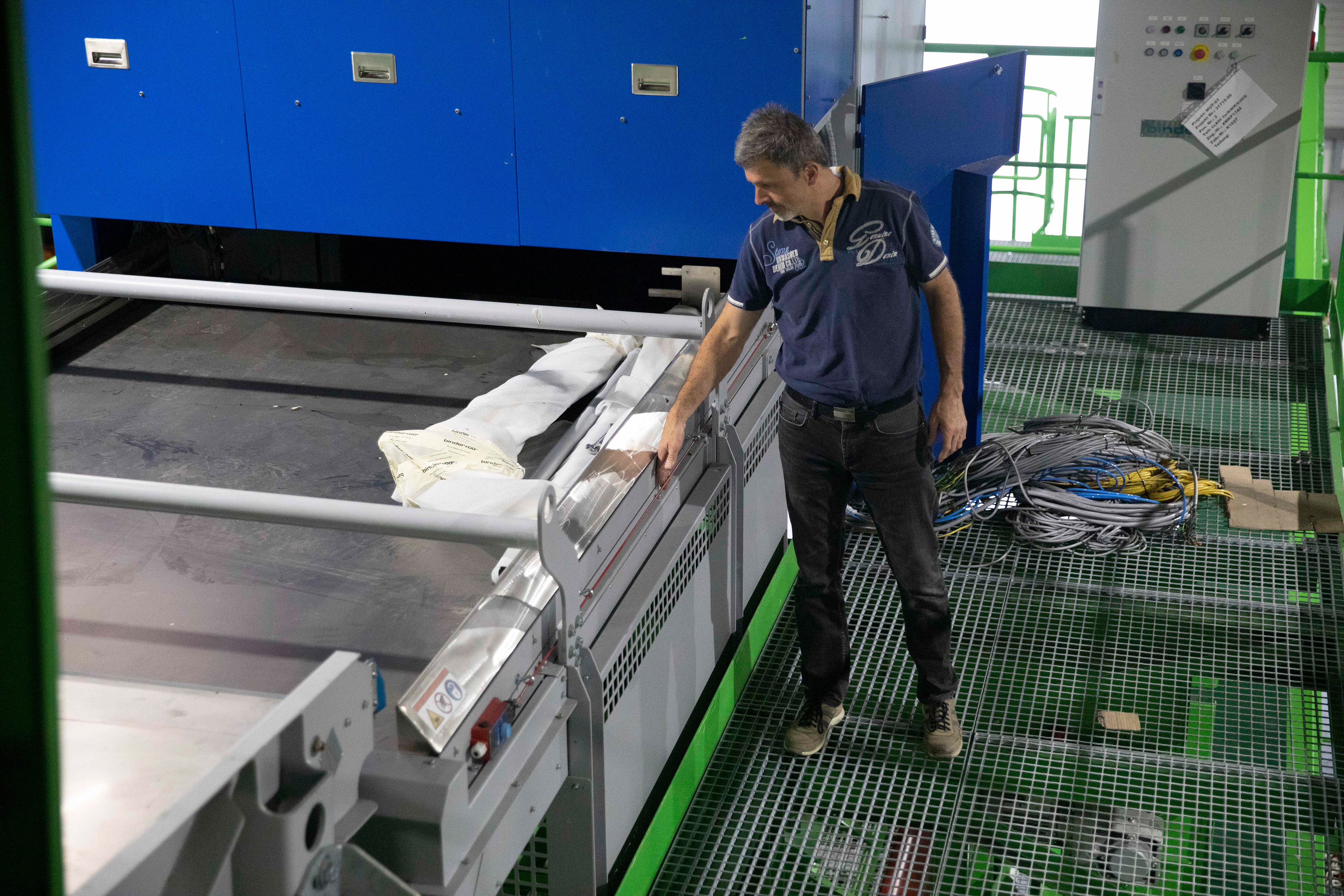
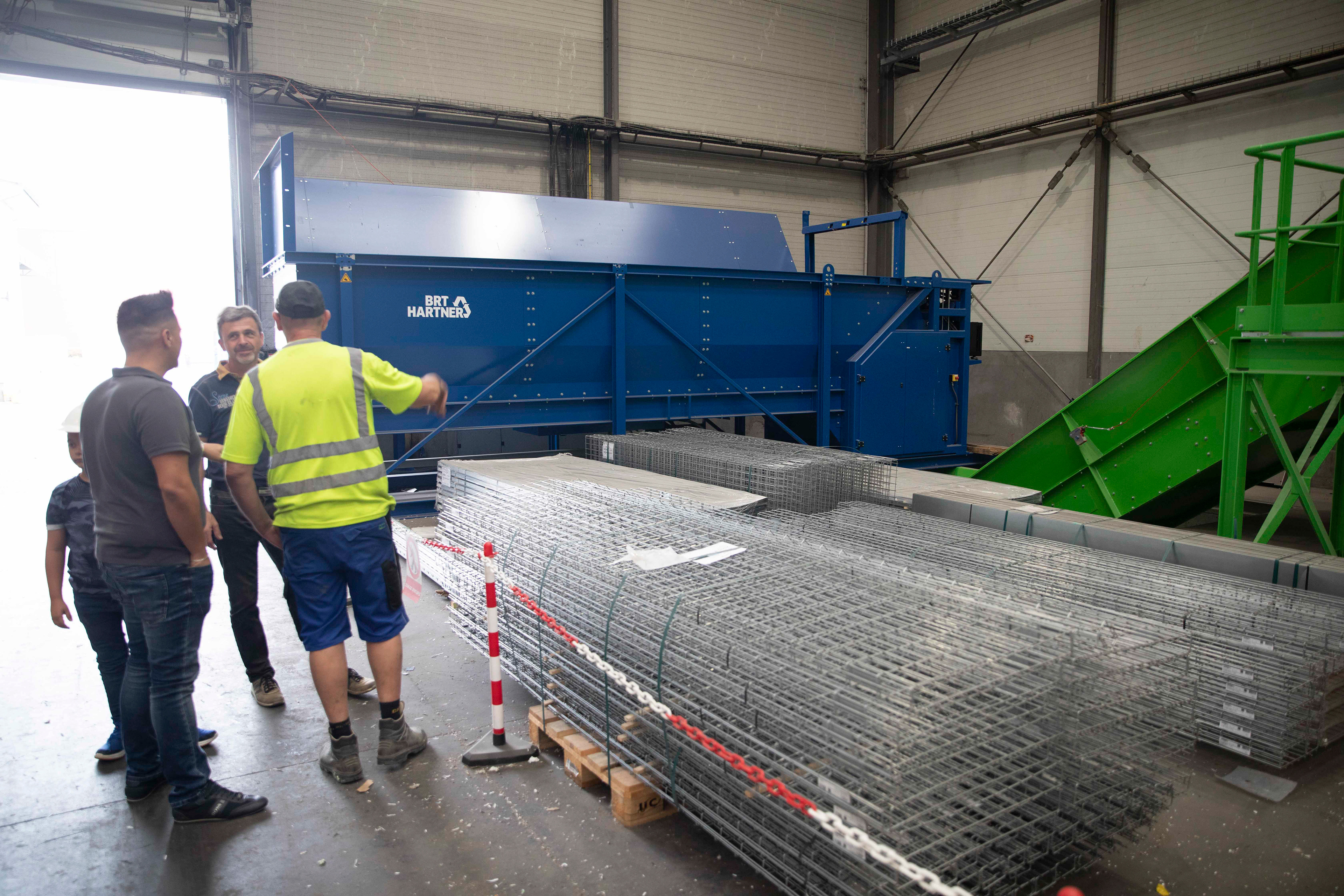
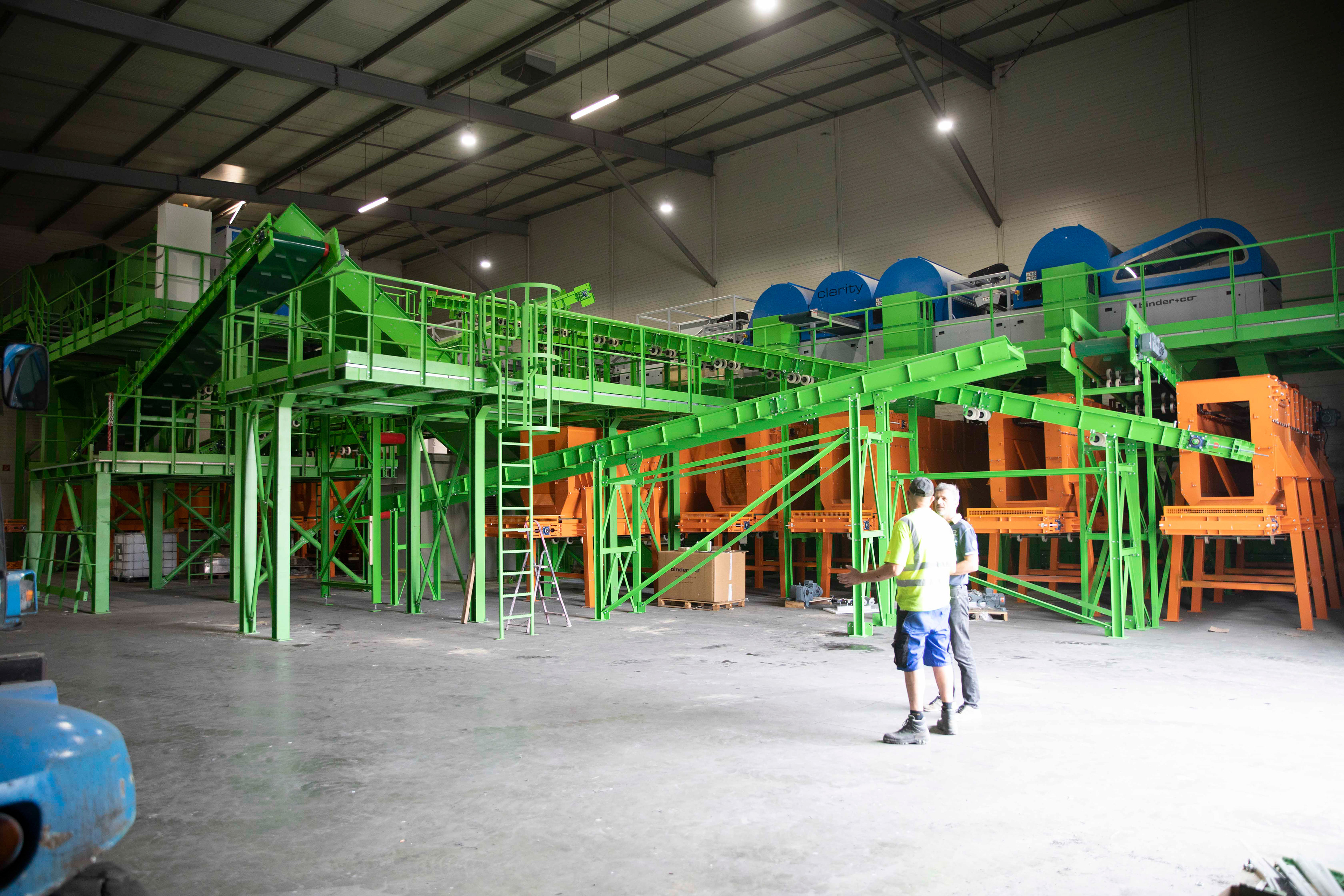
Collaboration Meets Improvisation
I worked closely with our core engineering team, external specialists, and local operators to rethink and refine the process flow. Whether we were tackling material throughput problems or redesigning certain modules entirely, my role evolved into one that combined engineering logic with a bit of creative firefighting.
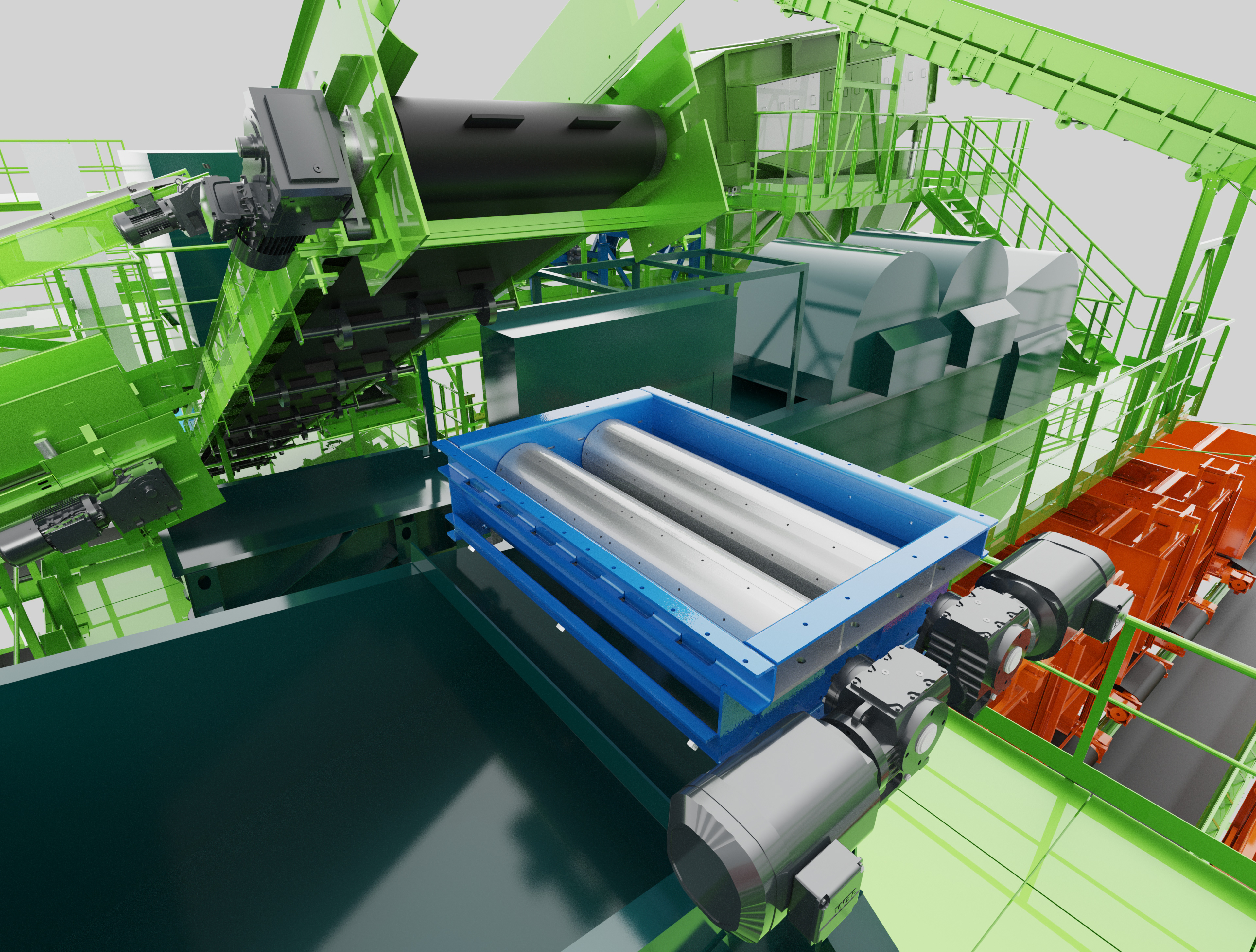
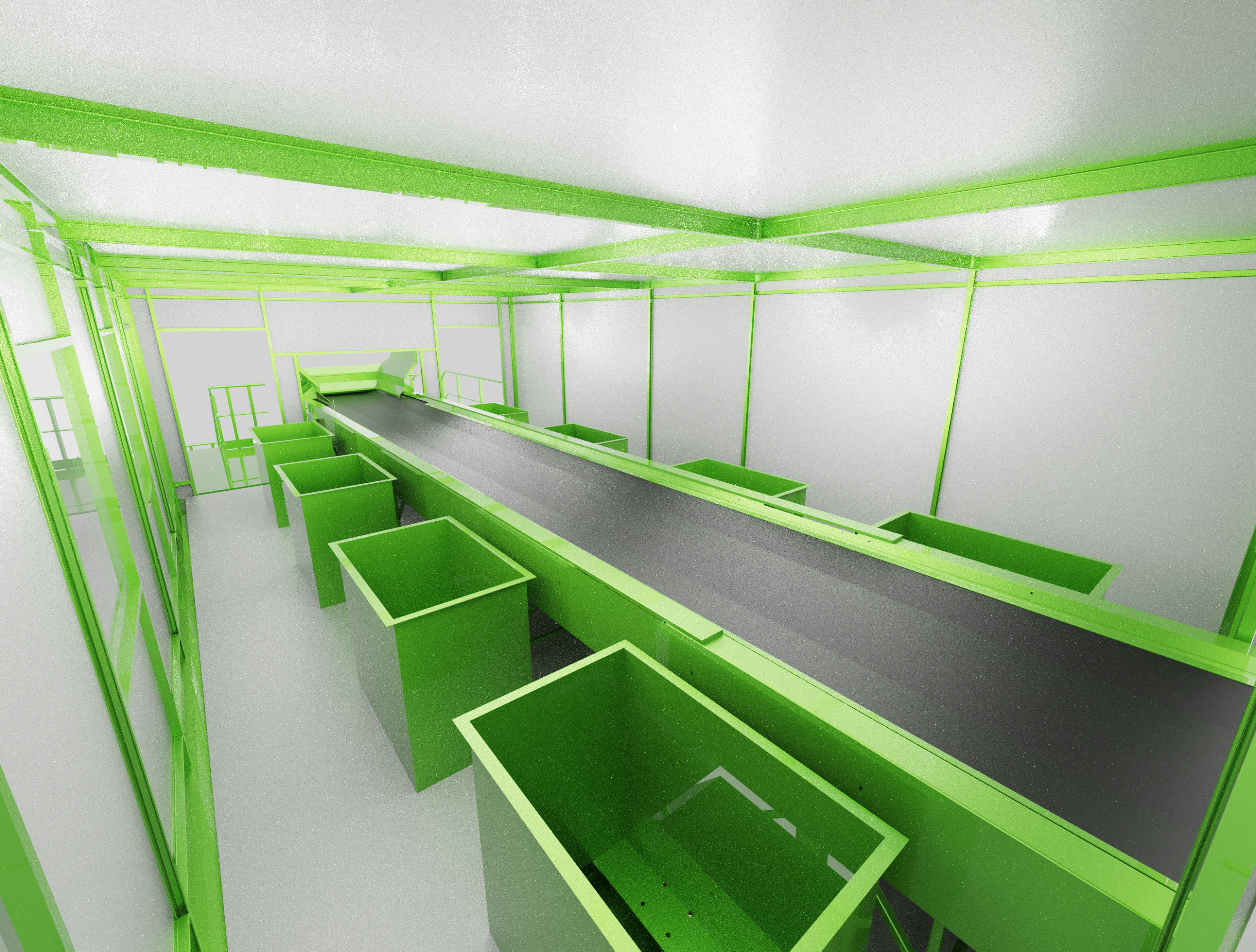
To support communication and planning, I created 3D renderings, visualizations, and animations of system components and workflows. These visuals weren’t just pretty – they helped align stakeholders, speed up troubleshooting, and even made their way into documentation and internal training.
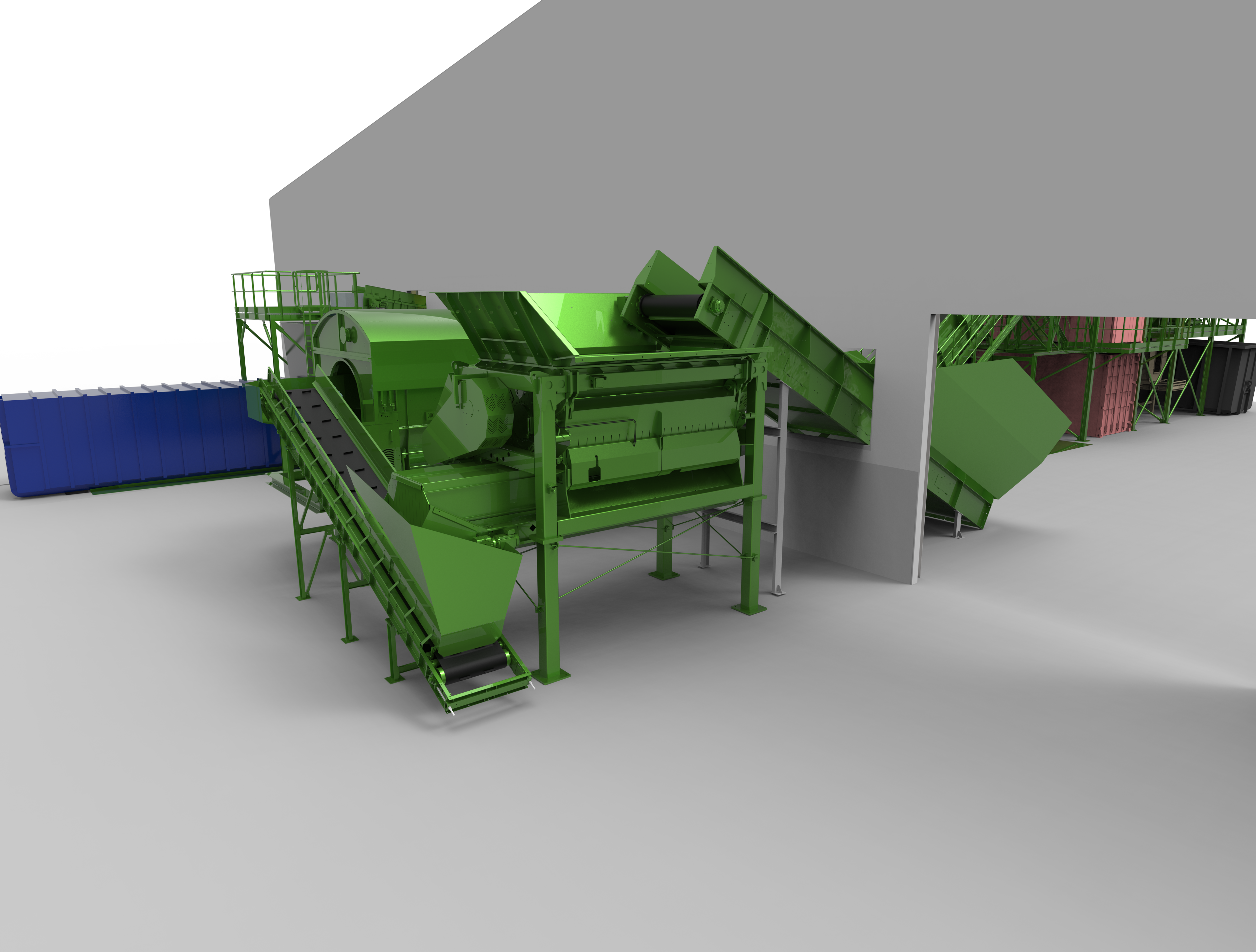